The Only Guide to Alcast Company
The Only Guide to Alcast Company
Blog Article
Not known Details About Alcast Company
Table of ContentsThe Basic Principles Of Alcast Company All about Alcast CompanySome Known Questions About Alcast Company.Some Known Details About Alcast Company The Single Strategy To Use For Alcast CompanyOur Alcast Company Statements
The refined difference depends on the chemical material. Chemical Contrast of Cast Light weight aluminum Alloys Silicon advertises castability by reducing the alloy's melting temperature level and boosting fluidness throughout casting. It plays an essential duty in permitting detailed mold and mildews to be filled properly. In addition, silicon adds to the alloy's toughness and use resistance, making it useful in applications where sturdiness is vital, such as vehicle components and engine elements.It likewise improves the machinability of the alloy, making it simpler to process into finished items. In this way, iron adds to the overall workability of light weight aluminum alloys. Copper increases electrical conductivity, making it useful in electrical applications. It additionally improves corrosion resistance and includes in the alloy's overall toughness.
Manganese adds to the toughness of light weight aluminum alloys and improves workability (Foundry). It is typically used in wrought light weight aluminum products like sheets, extrusions, and profiles. The visibility of manganese aids in the alloy's formability and resistance to splitting throughout fabrication procedures. Magnesium is a lightweight aspect that gives strength and influence resistance to aluminum alloys.
Alcast Company for Beginners
Zinc boosts the castability of light weight aluminum alloys and assists manage the solidification process throughout spreading. It enhances the alloy's stamina and firmness.
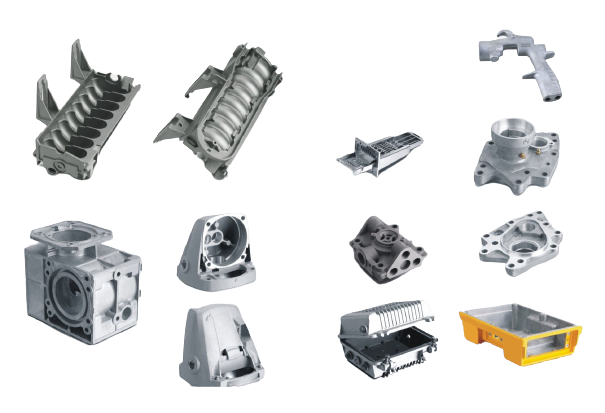
The key thermal conductivity, tensile strength, return toughness, and prolongation differ. Select ideal resources according to the performance of the target item generated. Amongst the above alloys, A356 has the greatest thermal conductivity, and A380 and ADC12 have the most affordable. The tensile limitation is the contrary. A360 has the finest yield strength and the highest prolongation price.
The 10-Second Trick For Alcast Company
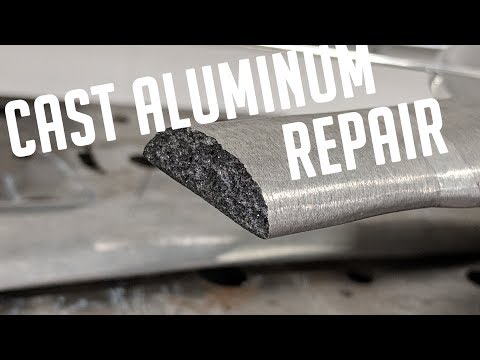
In accuracy spreading, 6063 is appropriate for applications where complex geometries and high-quality surface area coatings are extremely important. Instances consist of telecommunication rooms, where the alloy's exceptional formability allows for sleek and cosmetically pleasing styles while keeping architectural stability. Likewise, in the Lighting Solutions industry, precision-cast 6063 parts produce stylish and efficient lighting components that need elaborate shapes and excellent thermal efficiency.
It results in a better surface area finish and far better rust resistance in A360. The A360 exhibits premium elongation, making it ideal for facility and thin-walled components. In accuracy casting applications, A360 is fit for industries such as Customer Electronics, Telecommunication, and Power Tools. Its enhanced fluidness enables for detailed, high-precision elements like smartphone coverings and communication device real estates.
Facts About Alcast Company Uncovered
Its one-of-a-kind buildings make A360 a useful option for accuracy casting in these industries, improving product durability and top quality. aluminum casting manufacturer. Aluminum alloy 380, or A380, is a commonly used spreading alloy with a number of distinctive features.
In accuracy casting, aluminum 413 radiates in the Customer Electronic Devices and Power Devices industries. This alloy's exceptional deterioration resistance makes it a superb choice for outside applications, making sure durable, durable products in the view publisher site discussed industries.
Alcast Company Can Be Fun For Everyone
The light weight aluminum alloy you select will substantially influence both the casting process and the properties of the last product. Because of this, you should make your decision meticulously and take an enlightened strategy.
Determining the most ideal light weight aluminum alloy for your application will certainly imply considering a vast variety of features. The first classification addresses alloy features that affect the manufacturing procedure.
Some Ideas on Alcast Company You Need To Know
The alloy you select for die casting directly affects a number of elements of the casting process, like exactly how simple the alloy is to collaborate with and if it is prone to casting flaws. Hot splitting, also called solidification breaking, is a common die casting problem for aluminum alloys that can result in internal or surface-level rips or splits.
Particular light weight aluminum alloys are a lot more prone to hot breaking than others, and your selection needs to consider this. An additional typical problem found in the die spreading of light weight aluminum is die soldering, which is when the cast adheres to the die wall surfaces and makes ejection challenging. It can damage both the actors and the die, so you must search for alloys with high anti-soldering residential properties.
Corrosion resistance, which is currently a noteworthy feature of light weight aluminum, can vary substantially from alloy to alloy and is an essential particular to consider depending on the environmental problems your product will certainly be revealed to (aluminum foundry). Use resistance is another property generally looked for in light weight aluminum products and can differentiate some alloys
Report this page